Competitive Advantages: Understanding the various merits of Monolithic Casting Nylon (MC Nylon)
2025-06-11
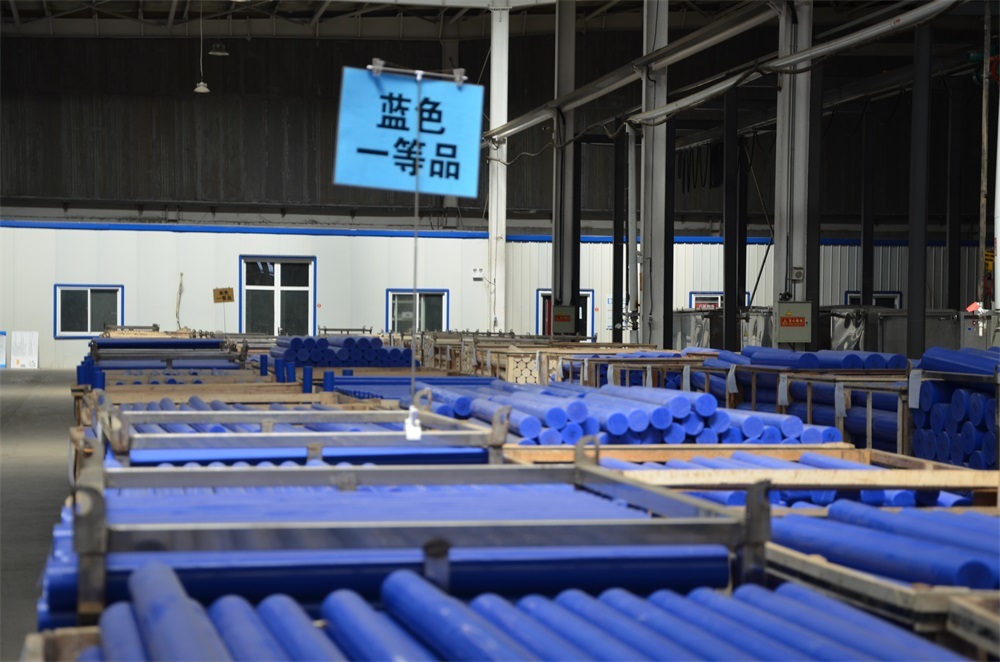
Gaining a Competitive Edge: Core Benefits of Using MC Nylon in Industrial Applications
When seeking materials that deliver durability, efficiency, and cost savings, Monomer Cast Nylon (MC Nylon) stands out as a leader. Its unique manufacturing process bestows upon it a range of properties that often surpass traditional engineering plastics and even metals in certain applications. For B2B decision-makers, understanding these advantages is key to unlocking higher performance and operational efficiency.
Core Advantages of MC Nylon Your Business Can Leverage:
The unique properties of MC Nylon translate into tangible benefits for a wide range of industrial applications.
● Lightweight Strength (High Strength-to-Weight Ratio): MC Nylon is significantly lighter than many traditional materials it replaces. Its specific gravity is only 1/7 that of steel and about 1/8 that of copper. This lightweight characteristic facilitates handling, installation, and is crucial for lightweighting equipment, thereby reducing energy consumption and inertial forces of moving parts. A 400 kg MC Nylon product has the volume equivalent to 2.7 tons of steel or 3 tons of bronze.
● Impressive Mechanical Strength: Despite its light weight, MC Nylon exhibits good tensile, compressive, and impact strength. The performance of certain grades is comparable to some metals. Typical tensile strength is in the range of 75-88 MPa, with some specific grades like MC901 (blue) known for higher toughness and fatigue resistance.
● Excellent Self-Lubricating Properties: MC Nylon inherently possesses a low coefficient of friction. This characteristic is particularly pronounced for modified grades, such as oil-impregnated MC Nylon, enabling effective operation under low or no lubrication. Its coefficient of friction is reported to be 8.8 times lower than steel and 8.3 times lower than copper. This reduces wear, minimizes maintenance, and lowers energy losses.
● Superior Abrasion Resistance: This is a hallmark characteristic of MC Nylon, making it ideal for manufacturing components such as gears, bearings, bushings, and rollers. In abrasive environments, it can significantly extend the service life of these parts, surpassing many metals and common engineering plastics. In some applications, it can increase component life by 4-5 times compared to metal parts.
● Good Chemical Resistance: MC Nylon exhibits good resistance to a variety of chemicals, including alkalis, alcohols, ethers, hydrocarbons, and lubricating oils. This makes it suitable for environments where chemical contact is an issue. However, it is important to note that its resistance to strong acids is weaker.
● Ease of Manufacturing Large, Complex Parts: The casting process allows MC Nylon to be made into large, thick-walled, or intricately shaped parts—ranging from a few kilograms to several tons. Compared to injection molding, tooling costs are relatively low, making it economical for small-to-medium production runs and custom parts.
● Vibration and Noise Reduction: MC Nylon has higher damping capacity than metals, meaning it can effectively absorb shocks and vibrations. This results in quieter machine operation, which benefits both equipment life and the work environment. For example, MC Nylon gears can reduce noise by 10-15dB.
● Good Electrical Insulation: MC Nylon exhibits good electrical insulation properties, with high volume and surface resistivity. This makes it suitable for electrical components, although its performance may be affected by moisture absorption.
Translating Advantages into Business Value
For purchasing managers and engineers, these advantages are more than just technical specifications; they translate into real business value:
● Reduced Costs: Achieved by reducing material weight (less transportation and handling costs), simplifying the machining of complex parts, extending part life, and reducing maintenance needs (especially lubrication).
● Enhanced Equipment Performance: Lighter parts can mean faster cycle times and lower energy consumption. Reduced friction and wear contribute to smoother operation and higher efficiency.
● Increased Uptime: More durable components and less frequent maintenance lead to reduced machine downtime.
● Improved Workplace Safety and Environment: Quieter operation and reduced need for manual lubrication contribute to a better work environment.
By considering MC Nylon, businesses can often achieve an excellent balance between performance, durability, and overall cost-effectiveness, especially when replacing traditional materials in demanding mechanical applications.
TAG:
Related News
Exploring the Power of Composite Materials in Modern Industry Solutions