MC Nylon In-depth Analysis: Understanding Key Performance Characteristics
2025-06-11
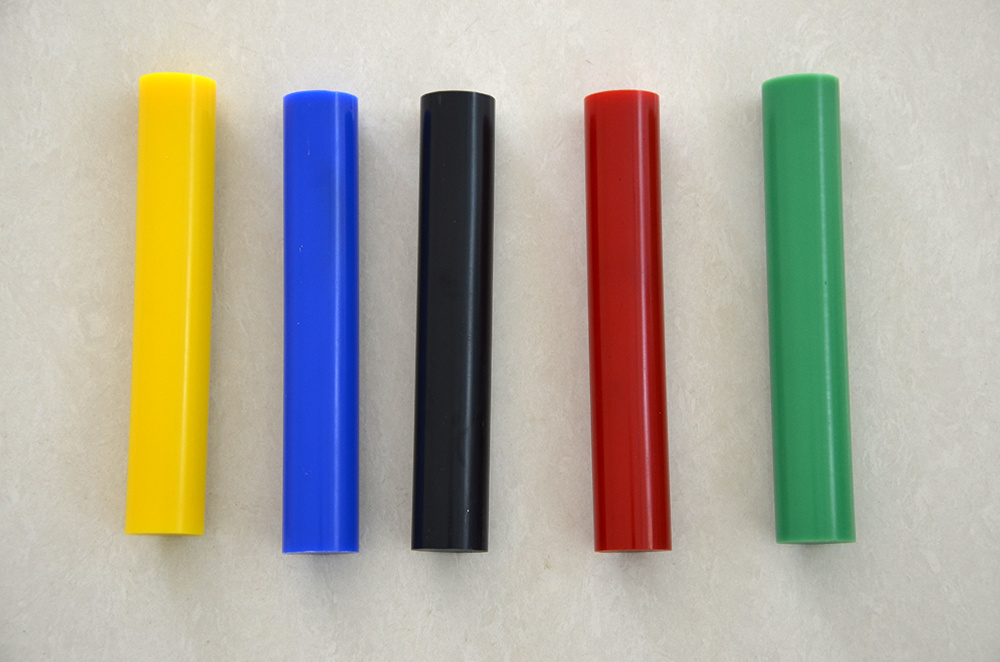
MC Nylon Performance Indicators: A Buyer's Guide to Mechanical, Thermal, and Chemical Properties
A thorough understanding of the key performance characteristics of Monolithic Cast Nylon (MC Nylon) is crucial when selecting it for industrial applications. These indicators determine how the material behaves under specific operating stresses, temperatures, and environmental exposures. This guide delves into the key mechanical, tribological (friction and wear), thermal, and chemical properties that B2B buyers must consider.
Mechanical Strength and Durability
The mechanical properties of MC Nylon are fundamental to its role as a structural and wear-resistant material.
● Tensile and Yield Strength: MC Nylon typically exhibits high tensile strength; unfilled grades such as MC901 usually fall within the range of 80-100 MPa, while some sources indicate a general tensile strength of 75-88 MPa for MC Nylon. This allows it to withstand significant pulling forces.
● Impact Strength: This measures toughness, or the ability to resist sudden loads. MC Nylon possesses good impact resistance, especially the toughened grades, maintaining performance even at low temperatures. MC901 (blue) modified nylon is claimed to have higher toughness than ordinary cast nylon. Simply supported beam impact strength (notched) can reach 4-8 kJ/m², while some tests show cantilever beam un-notched impact strength of 9.3 kJ/m².
● Hardness: Usually measured by Shore D or Rockwell hardness. MC Nylon has high surface hardness (e.g., Shore D hardness of 80-85 and Rockwell hardness of R110-R115 for MC901), resisting indentation and wear.
● Flexural Strength and Modulus: Flexural strength reflects the ability to resist bending failure (typically around 100-150 MPa for unmodified MC Nylon), while flexural modulus (approximately 3-4 GPa) reflects its stiffness.
● Fatigue Strength: Crucial for components like gears and bearings that experience cyclical loading; modified MC Nylon (such as MC901 blue) performs better in this aspect.
Procurement Insight: Match the grade-specific mechanical properties (tensile, impact, fatigue strength) with the forces your component will endure.
Friction and Wear (Tribological) Performance
MC Nylon is known for its self-lubricating and wear-resistant properties, key to its "plastic-for-metal" capabilities.
● Coefficient of Friction: Significantly lower than metals such as steel (8.8 times lower) and copper (8.3 times lower). MC Nylon modified with oil or solid lubricants can further reduce the coefficient of friction by 50% or more.
● Wear Resistance: Exhibits excellent wear resistance, outlasting many metals and common plastics under the same conditions. Modified grades (oil-filled, molybdenum disulfide-filled) offer significant improvements (e.g., oil-filled grades can increase wear resistance tenfold).
● PV Limit: The product of pressure (P) and velocity (V), a key indicator for bearing materials. MC Nylon, especially grades containing solid lubricants, has a high PV value (5 times higher than ordinary cast nylon), suitable for high-load, high-speed sliding applications.
Procurement Insight: For moving parts (bearings, gears, sliders), prioritize low friction and high wear resistance. Modified grades enable oil-free operation or extended lubrication intervals.
Thermal Stability and Behavior
The performance of MC Nylon at different temperatures determines its application range.
● Heat Deflection Temperature (HDT): The temperature at which the material reaches a specified deflection under a specified load. The HDT of MC Nylon typically ranges from 150-200°C, but under a 1.8 MPa load, standard grades are usually around 90-110°C; some specific tests even show 67°C.
● Continuous Use Temperature: The highest temperature at which the material can be used in air for an extended period without significant performance degradation. The continuous use temperature of general MC Nylon is approximately 90-120°C (e.g., MC901 can reach 120°C). Special heat-resistant grades (such as brown MC602) can reach 150°C or even higher.
● Coefficient of Linear Thermal Expansion (CLTE): Relatively high, approximately (8-10) x 10⁻⁵/K, much greater than metals. This means that dimensional changes must be considered in the design in environments with significant temperature variations. Some sources list the value as 96.5 x 10⁻⁶ K⁻¹.
Procurement Insight: Select the grade based on the actual operating temperature. Be sure to design for thermal expansion, especially in precision components or where temperature fluctuations are significant.
Chemical and Environmental Resistance
Understanding the interaction between MC Nylon and its environment is crucial.
● Oil, Solvent, and Alkali Resistance: Exhibits good resistance to most organic solvents, greases, fuels, and alkaline chemicals.
● Acid Resistance: Generally poor resistance to strong acids, especially inorganic acids; not recommended even at low concentrations and room temperature. It has some resistance to weak acids.
● Water Absorption and Dimensional Stability: A major challenge. MC Nylon absorbs moisture, especially in humid conditions or in contact with water, leading to dimensional swelling and changes in mechanical properties (reduced strength/hardness, possibly increased toughness). Saturation water absorption can reach 6-8%. Some sources indicate lower 24-hour water absorption (0.2-0.3% or 0.8%), with saturation water absorption around 6.5%. This issue must be managed through design allowances, pre-treatment, or selection of grades with lower water absorption.
● Weather Resistance: Standard MC Nylon has generally poor weather resistance; prolonged exposure to UV light causes degradation. Grades with added UV stabilizers or graphite modifications (such as MC801) significantly improve their outdoor performance.
Procurement Insight: Clarify the chemical environment, humidity, and UV exposure. For humid conditions, prioritize dimensional stability or take mitigating measures. Avoid use in strong acid environments.
Machinability and Other Key Properties
Machinability: Excellent. Standard metalworking techniques (turning, milling, drilling) can be used for precision machining. Due to its poor thermal conductivity, heat dissipation must be considered during processing to prevent melting.
Electrical Insulation: Good insulation properties, but these properties decrease with moisture absorption.
By carefully evaluating the match between these performance parameters and the needs of a specific application, companies can confidently select the most suitable MC nylon grade to ensure optimal functionality and service life.
TAG:
Related News
Exploring the Power of Composite Materials in Modern Industry Solutions